Wax plays a hidden role in countless products we use every day. Beyond candles and crayons, waxes improve production and function across industries. The variety of natural and synthetic waxes creates options for specialized applications. Making an informed wax choice aligns with manufacturing goals. Consider these key factors when selecting the best wax for your needs.
Look at Your Application
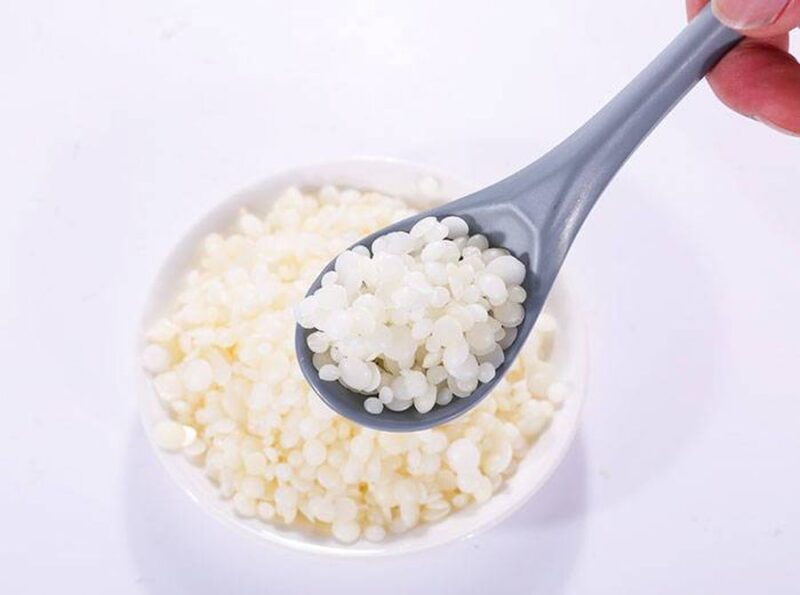
Every wax formulation aims to enhance certain properties. Is the priority temperature stability, moisture resistance, controlled release rates or surface finish? The manufacturing application guides ideal wax traits.
For example, microcrystalline wax withstands high heat in metal castings without burning. Paraffin’s moisture resistance makes an excellent moisture barrier in corrugated boxes and food packaging. Polyethylene wax emphasizes slippery surface coating for composites used in snow sports equipment. According to the experts at Trecora, application demands determine wax selection criteria like melting point, hardness, flexibility and water repellency.
Consider Processing Method Factors
Ease of use during processing also affects wax choice. Production method requirements like temperature thresholds, viscosity limits and bonding behaviors impact options.
Will the wax be integrated into liquid solution or molten state? Wax viscosity at heated temperatures enables either spray-on or dipping uses. Slow setup time is crucial for manufacturing steps like hand dipping. Faster viscosity change may suit spray nozzles in automated lines.
Evaluate Performance Properties Needed
The role wax plays in end-product performance also weighs on material selection. Which functional enhancements like weatherability, friction modification or crack healing are sought? Target performance goals help identify the best wax or wax blend formulation.
For example, petroleum-based slack wax boosts UV resistance in outdoor wood sealants. Oxide nanoparticle infused paraffin wax enhances scratch healing properties in protective automotive coatings. Polyethylene wax boosts scuff resistance and raises blurring points in floor polishes for durability despite traffic. Defining functional metrics expected from the wax additive focuses selection criteria.
Understand Economic Balance
Finally, wax choice affects operational costs across purchasing and production. Prices fluctuate globally based on crude oil costs, harvest yields, and supply chain factors. Comparing wax options on both unit pricing and performance per pound identifies potential savings.
Enhanced manufacturing efficiency from the optimized wax pays dividends over time. For example, polyethylene wax may carry higher upfront costs than paraffin but boost total productivity through faster processing speeds or enabling automated production. Weigh lifetime value against price point when choosing manufacturing ingredients.
Wax Modifications Expand Options
The customization possible with wax also empowers specialty formulation for niche applications. Techniques like polymer blending, oxidation and chemical infusion adapt base waxes to achieve ideal properties.
Polymer Modified Wax
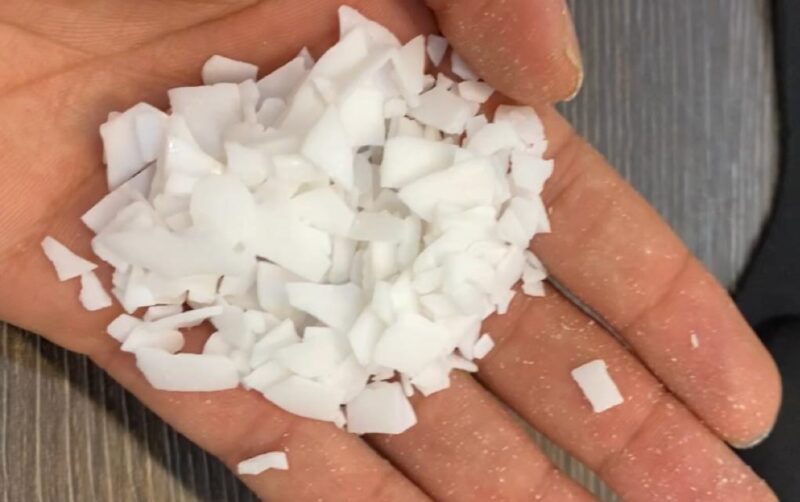
Introducing plastics like polyethylene into wax changes structure and improves performance. For example, mixing polyethylene into paraffin wax raises melting point for candles and 3D printing uses. Polymer wax resists oil migration in cosmetic and food applications. It also makes excellent hot melt adhesive for binding wood composites because of adjustable flexibility and bonding behaviors.
Oxidized Wax
Oxidation treatment alters wax at the molecular level to enhance specific traits like hardness and melt viscosity. Oxidizing plant-based carnauba wax via sunlight, air and chemical exposure transforms its viscosity profile – ideal for tropical location manufacturing. Oxidized paraffin wax boosts utility in rubber and vinyl production through tailored melt flow rates.
Chemically Infused Wax
Changes at an elemental level amplify characteristics like strength and conductivity. Introducing graphene to beeswax reinforced 3D printed structures with excellent fracture resistance. Scattering carbon nanotubes through paraffin wax builds electrically conductive additions for smart materials and sensors.
Conclusion
Choosing the optimized wax empowers manufacturing processes to run smoothly, efficiently and economically while enabling exceptional finished product performance. Consider both off-the-shelf and customized waxy solutions when evaluating ingredient selection for your production needs.